From Concept to Creation: Get Started in Manufacturing Today
At the core of any manufacturing process lies its concept. Whether you’re producing something entirely new or replicating an existing one, understanding its inner workings is paramount for success. This blog post will help you develop your concept into a plan for production – including selecting materials, calculating costs, and setting timelines among other key considerations. Heading on this exciting journey could be the start of maybe a valuable and strong international business.
1) Selecting Appropriate Materials
One of the first steps of manufacturing is selecting appropriate materials to produce your product. You should take several factors into consideration when making this choice, including cost, quality, durability, availability, and cost-effectiveness. Once you’ve identified suitable material(s), you can then move on to designing and prototyping.
2) Designing and Prototyping:
Designing and prototyping are fundamental processes in manufacturing. Prototyping allows you to test various designs and concepts prior to committing production costs, helping ensure that the design works as anticipated before mass-producing it. By making a prototype of your product design you can identify any issues or make necessary changes as soon as necessary.
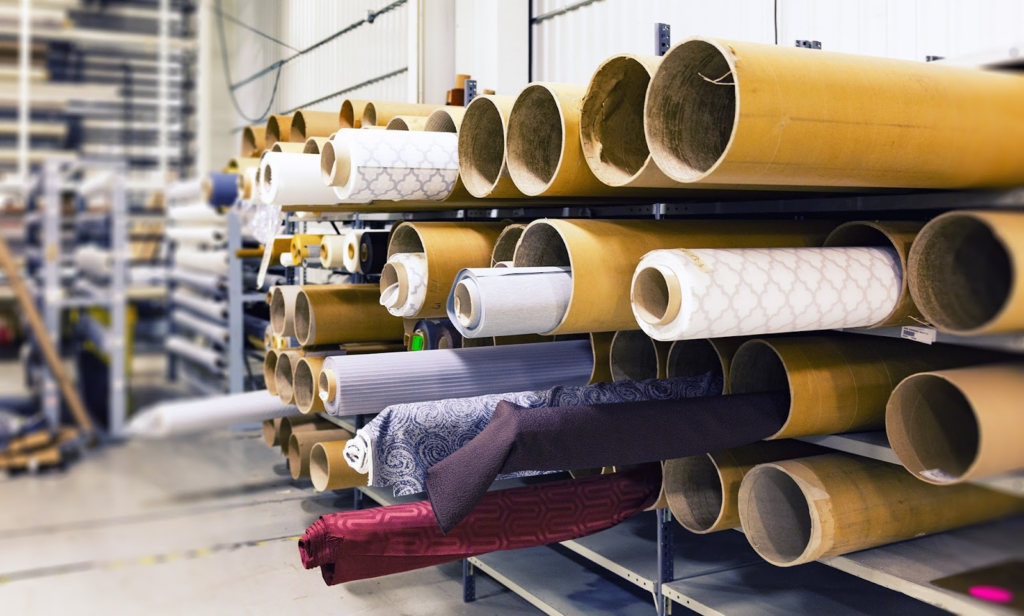
3) Estimating Costs & Establishing a Timeline:
Establishing costs accurately is an integral component of production. You will need to take into account materials, labor costs, overhead expenses such as rent and utilities as well as any specialized equipment necessary for production when creating your cost estimates. Once all expenses have been estimated and allocated a timeline should each task be completed on schedule for uninterrupted production.
4) Quality Control and Testing:
Quality control and testing are integral parts of manufacturing. By adhering to high standards for your product before it reaches customers, quality control helps ensure its satisfaction; quality testing allows manufacturers to detect any potential issues with their product that might cause customer dissatisfaction or recalls.
5) Finalizing and Shipping:
After all previous steps have been completed successfully, it’s time to finalize and ship your product. Depending on the nature of your business, this may involve packaging, labeling, and shipping it directly to customers or stores. Logistics play an essential part in this process as customers should receive their products on time and without damage; to ensure this occurs smoothly it’s essential that every step in this process be planned out carefully, hiring professionals such as IFL to assist, in order to provide customers with quality products which meet expectations.
6) Documents and Reviewing:
Once your manufacturing process is completed, you must document and review every step you took to track potential problems or ensure quality assurance. By reviewing processes and making any necessary modifications where needed, future productions should run more smoothly. Take time to make sure that everything is documented and every step has been followed, you need to have records of everything.
In conclusion, following these steps from concept to creation will help get you started on the path toward successful manufacturing today! With the right materials, design plans, cost estimates, timelines, and quality control measures in place, you’ll be able to produce a product that meets your customers’ needs and expectations.